Yes, you can weld 304 to 316 as they are both austenitic stainless steels with similar welding characteristics. Welding is a widely used method in various industries for joining metal components.
When it comes to welding stainless steel, compatibility between different grades becomes an important consideration.
In this case, welding 304 to 316 stainless steel is possible due to their similar characteristics as both are austenitic stainless steels. These types of stainless steels offer excellent corrosion resistance, high strength, and good weldability.
However, it is essential to use appropriate consumables and welding techniques to ensure a successful weld.
This article will explore the compatibility of welding 304 to 316 stainless steel and provide insights into the process, precautions, and considerations for achieving a strong and durable weld.
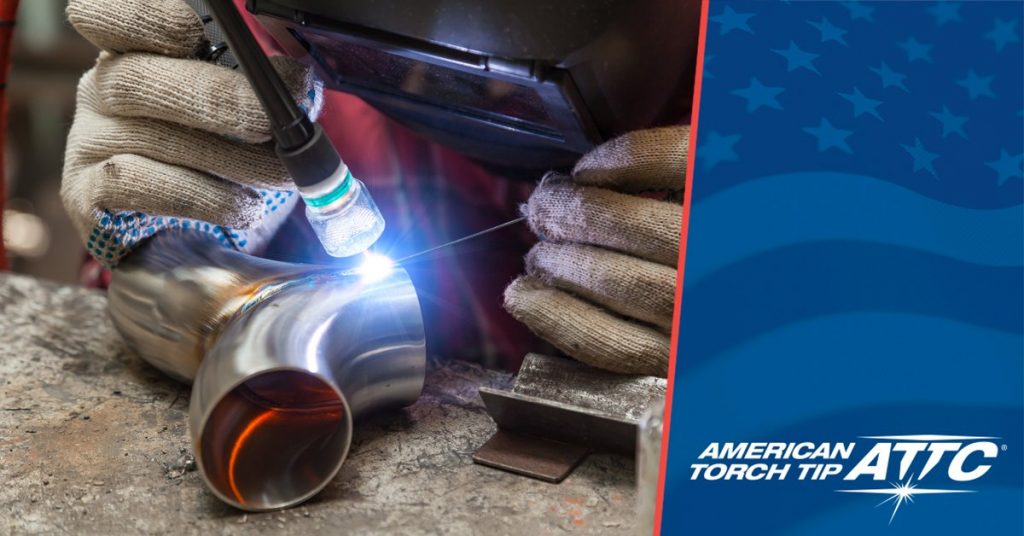
Contents
Understanding 304 And 316 Stainless Steel
Chemical Composition
304 Stainless Steel: Contains 18% chromium & 8% nickel.
316 Stainless Steel: Contains 16% chromium & 10% nickel.
Properties
- 304 Stainless Steel: Good corrosion resistance, suitable for indoor use.
- 316 Stainless Steel: Higher corrosion resistance, ideal for marine environments.

Can You Weld 304 To 316 Stainless Steel?
When it comes to welding stainless steel, one common question that often arises is whether it is possible to weld 304 stainless steel to 316 stainless steel.
In this article, we will explore this topic and discuss the challenges of welding dissimilar stainless steels and the considerations to keep in mind when welding 304 to 316 stainless steel.
Challenges Of Welding Dissimilar Stainless Steels
Welding two different grades of stainless steel, such as 304 and 316, involves several challenges. One of the main challenges is the difference in composition between these two stainless steels.
While both 304 and 316 stainless steel alloys contain nickel, chromium, and molybdenum, their proportions can vary. 304 stainless steel has a higher amount of chromium and nickel compared to 316 stainless steel, which means that it is generally more resistant to corrosion.
On the other hand, 316 stainless steel has a higher amount of molybdenum, which enhances its resistance to pitting and crevice corrosion.
These differences in composition can affect the weldability of dissimilar stainless steels. The dissimilar weld joint may experience issues such as intergranular corrosion, cracking, and reduced corrosion resistance.
Considerations For Welding 304 To 316 Stainless Steel
When welding 304 stainless steel to 316 stainless steel, there are a few considerations that can help ensure a successful weld:
- Choose the right filler metal: When welding dissimilar stainless steels, it is crucial to select a filler metal that matches the higher grade stainless steel. In this case, a filler metal with a higher alloy content, such as ER316, is typically used to weld 304 stainless steel to 316 stainless steel. This helps maintain the corrosion resistance of the joint.
- Control the heat input: Stainless steel is sensitive to heat input during welding. Excessive heat can cause distortion, reduce corrosion resistance, and lead to weld defects. Therefore, it is essential to control the heat input by using proper welding techniques such as preheating and post-weld heat treatment.
- Ensure proper preparation: Before welding, it is crucial to properly clean and prepare the surfaces to be joined. This includes removing any contaminants, such as dirt, grease, or oxide layers, which can affect the quality of the weld.
In conclusion, while it is possible to weld 304 stainless steel to 316 stainless steel, there are challenges that need to be considered.
By carefully selecting the right filler metal, controlling the heat input, and ensuring proper surface preparation, you can achieve a strong and corrosion-resistant weld between these dissimilar stainless steels.
Expert Tips For Seamless Welding
Preparation
Before welding 304 to 316 stainless steel, ensure surfaces are clean to prevent contamination. Use acetone or a similar solvent to remove any grease, oil, or dirt. Additionally, ensure the base metals are free from oxide layers and scale to ensure a strong weld joint.
Selection Of Filler Metal
Choose a filler metal that is specifically designed for joining stainless steel, such as an austenitic stainless steel filler material containing molybdenum. The filler metal’s composition should match the base metals as closely as possible to ensure a seamless and strong weld.
Appropriate Welding Technique
Employ the TIG welding technique for welding 304 to 316 stainless steel as it provides better control and precision.
Adjust the welding parameters to match the specific grades and thicknesses of the base metals. Maintain a steady arc and utilize a back purge of argon gas to prevent oxidation on the backside of the weld.
Common Welding Techniques For 304 To 316 Stainless Steel
Welding 304 to 316 stainless steel combines two common techniques: TIG welding and filler metals, creating a strong bond. By understanding the differences in composition, welders can effectively join these two stainless steel grades for various applications.
When welding 304 to 316 stainless steel, specific techniques must be applied to ensure a strong bond. Here are the common methods to consider:
Quality Control And Inspection
When it comes to welding 304 to 316, quality control and inspection are crucial to ensure the integrity of the weld joint. The process involves careful examination of the materials and meticulous attention to detail to guarantee a strong and durable bond between the two stainless steel grades.
When it comes to welding 304 and 316 stainless steel, quality control and inspection play a critical role in ensuring the strength and durability of the weld joint. Both visual inspection and various testing methods are employed to ensure the weld meets the required standards and specifications.
Visual Inspection
The first step in quality control is visual inspection, where the weldment is carefully examined for any visible defects or irregularities. This includes checking for proper penetration, uniformity, and the absence of cracks, porosity, or incomplete fusion.
During visual inspection, welders and inspectors use their expertise and specialized tools to assess the appearance and overall integrity of the weld.
They pay close attention to the shape, size, and contour of the weld, as well as the color and uniformity of the heat-affected zone.
Destructive Testing
Ensuring the strength and structural integrity of the weld joint often requires destructive testing methods. These tests involve subjecting the weldment to extreme conditions to determine its maximum load capacity, ductility, and resistance to failure.
Destructive testing methods for welded stainless steel joints may include tension tests, where the weld is pulled in opposite directions to measure its strength.
Bend tests are also commonly performed, where the weld is bent over a specified radius to assess its ductility and the absence of cracks or defects.
Non-destructive Testing
In addition to destructive testing, non-destructive testing methods are utilized to evaluate the quality of the weld joint without causing any damage. These methods are crucial for ensuring the reliability and long-term performance of the weld.
Non-destructive testing techniques commonly employed in weld inspections include liquid penetrant testing, where dye is applied to the weld and any surface defects are highlighted, and magnetic particle testing, which uses magnetic fields and iron particles to detect surface and near-surface defects.
Other non-destructive testing methods include ultrasonic testing, where high-frequency sound waves are used to detect internal defects, and radiographic testing, which involves the use of X-rays or gamma rays to produce images of the weld joint and identify any hidden flaws or defects.
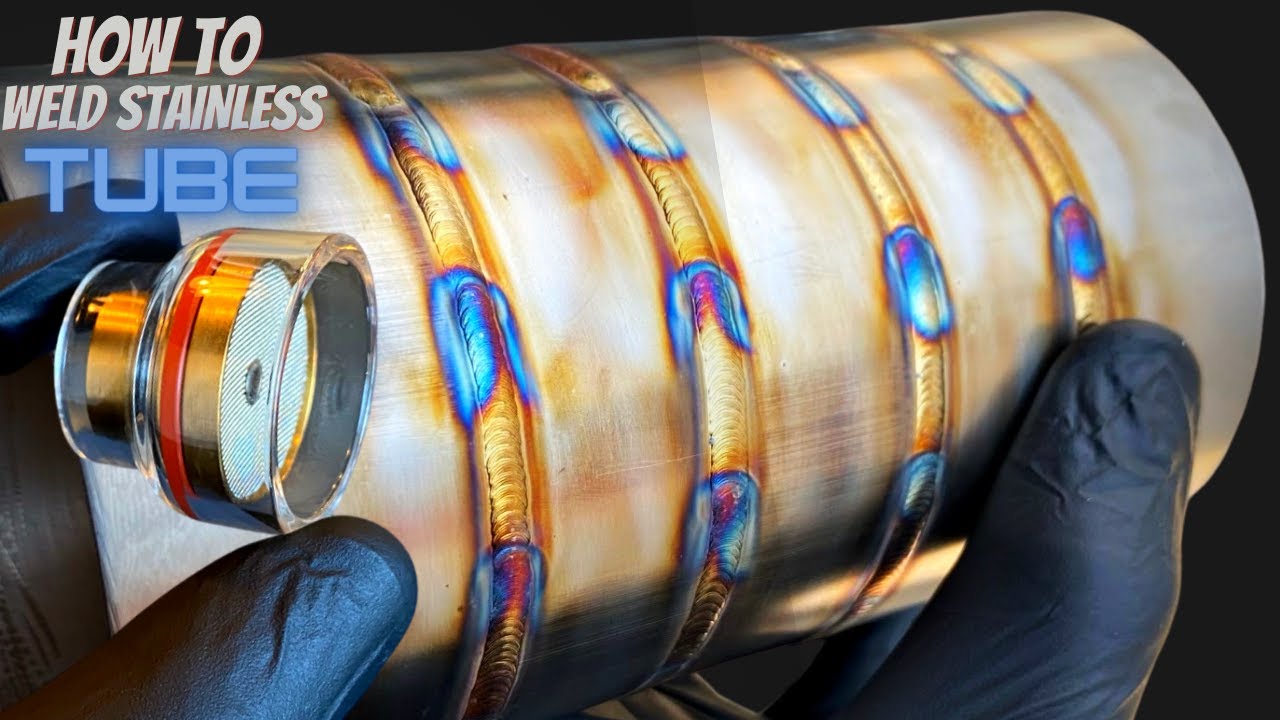
Applications And Industries
When it comes to welding stainless steel, understanding the compatibility between different grades is crucial. In this blog post, we will explore the application and industry-specific uses of welding 304 and 316 stainless steel.
Food And Beverage
Stainless steel plays a vital role in the food and beverage industry, where hygiene and cleanliness are of utmost importance. Both 304 and 316 stainless steel offer excellent corrosion resistance, making them suitable for a range of applications.
Here are some examples:
- Food processing equipment
- Brewing tanks and fermentation vessels
- Dairy processing equipment
- Conveyor systems
With their high corrosion resistance and compatibility with food-grade materials, both 304 and 316 stainless steel are commonly used in food and beverage manufacturing.
Pharmaceutical
The pharmaceutical industry demands materials that can withstand harsh environments and rigorous cleaning processes.
Stainless steel, especially grades 304 and 316, fulfills these requirements and finds extensive use in pharmaceutical applications, including:
- Vessels and tanks for drug manufacturing
- Piping systems for liquid and gas transport
- Pharmaceutical machinery components
- Lab equipment and bioreactors
Due to their excellent corrosion resistance, stainless steel welds between 304 and 316 are suitable for pharmaceutical applications that require resistance to corrosive chemicals and frequent cleaning.
Chemical Processing
Chemical processing environments can be highly corrosive, posing a challenge for materials to endure. Both 304 and 316 stainless steel offer exceptional resistance to a wide range of chemical compounds.
Consequently, they find widespread use in chemical processing industries, such as:
- Pressure vessels and reactors
- Piping systems
- Heat exchangers
- Tanks and storage containers
The compatibility between 304 and 316 stainless steel allows for effective welds in chemical processing applications without compromising the integrity of the finished product.
Marine
Marine environments expose materials to the corrosive effects of saltwater, constant moisture, and unpredictable weather conditions. Stainless steel, especially grades 304 and 316, are highly resistant to corrosion in marine environments.
This makes them ideal for various marine applications, including:
- Boat and yacht fittings
- Underwater structures
- Marine hardware
- Decking and handrails
The ability to weld 304 to 316 stainless steel offers fabricators and engineers the flexibility to design and construct durable structures in the demanding marine industry.
Frequently Asked Questions For Can You Weld 304 To 316
Is 304 And 316 Stainless Steel Compatible?
Yes, 304 and 316 stainless steel are compatible due to their similar properties. They can be used together without causing galvanic corrosion.
What Filler For 304 To 316?
Use 316 filler when welding 304 stainless steel for optimal corrosion resistance.
Can You Weld Different Types Of Stainless Steel?
Yes, you can weld different types of stainless steel, but it is important to choose the appropriate filler metal for compatibility.
Can You Weld 304 To 17 4?
Yes, you can weld 304 stainless steel to 17-4 stainless steel. It is essential to use the appropriate filler metal for a successful weld.
Conclusion
Achieving successful welds between 304 and 316 stainless steel can be challenging but possible. Understanding their differences and following precise welding techniques is crucial.
With proper preparation and skill, you can create strong and durable welds that meet your project needs. Mastering this skill opens up a world of possibilities.