To calibrate a welding machine, follow these steps: 1) Set the voltage and wire feed speed according to the manufacturer’s recommendations. 2) Use a calibrated multimeter to measure the voltage.
Open the welding machine’s panel and adjust the voltage until it matches the desired reading. Calibration of welding machines ensures accurate and consistent welding performance. Welding machines are essential tools in various industries, used for joining metals together efficiently.
However, to ensure their optimum performance, calibration is necessary. By calibrating a welding machine, operators can determine if the machine is producing the correct voltage and wire feed speed for the desired weld.
This process guarantees accurate and consistent weld quality, reducing the chances of defects or weak joints. We will provide a step-by-step guide on how to calibrate a welding machine, helping professionals and enthusiasts achieve precise results in their welding projects.
Contents
Importance Of Calibration
Calibrating a welding machine is crucial for ensuring safety and achieving precise welding results. It involves aligning and adjusting the equipment to perform at its optimal capacity, ultimately enhancing the quality of the welding process.
Ensuring Safety
Calibrating a welding machine helps in maintaining safe working conditions by ensuring that the equipment functions correctly. This reduces the risk of accidents and injuries to the welder and others in the vicinity.
Achieving Precise Welding Results
By calibrating the welding machine, precise welding results can be achieved consistently. This ensures that the welds are of high quality and meet the required specifications, leading to better overall project outcomes.
Understanding Welding Machine Calibration
What Is Welding Machine Calibration?
Welding machine calibration is the process of aligning and adjusting the settings of a welding machine to ensure it performs accurately and efficiently.
The calibration procedure involves adjusting the voltage, current, wire feed speed, and other parameters to meet the specific requirements of a welding project.
Types Of Welding Machine Calibration
There are various types of welding machine calibration, each designed to optimize the performance of specific welding processes. These include:
- Resistance Spot Welding Calibration
- Gas Metal Arc Welding (GMAW) Calibration
- Gas Tungsten Arc Welding (GTAW) Calibration
- Shielded Metal Arc Welding (SMAW) Calibration
Each type of calibration is tailored to the unique requirements of the welding process, ensuring precise and consistent results.
Tools Needed For Calibration
Welding machine calibration is essential for maintaining accurate and precise welding operations. To perform this task, several tools are required to ensure the welding machine is functioning correctly. Let’s explore the necessary tools for calibration.
Multimeter
Using a multimeter is crucial for measuring the voltage, current, and resistance of the welding machine. This tool helps in identifying any discrepancies in the electrical parameters, ensuring the machine operates optimally.
Calibration Standards
Calibration standards such as certified test gauges and load cells are essential for validating the accuracy and performance of the welding machine. These standards serve as benchmarks for the calibration process, guaranteeing precise results.
Welding Machine Manual
The welding machine manual is a valuable resource that provides detailed instructions on calibration procedures specific to the model. It outlines the recommended calibration methods and parameters, serving as a reference guide for the process.
Step-by-step Calibration Process
When it comes to welding, precision and accuracy are paramount. Proper calibration of a welding machine ensures that the voltage and amperage are set to the appropriate levels, resulting in high-quality, consistent welds.
Here, we will walk you through the step-by-step calibration process, covering important aspects such as disconnecting power, adjusting voltage and amperage, and testing the calibration.
Disconnecting Power
First and foremost, safety is crucial when calibrating a welding machine. Before beginning the calibration process, always ensure that the power source to the welding machine is completely disconnected. This can be achieved by unplugging the machine or turning off the power at the circuit breaker.
Adjusting Voltage And Amperage
Once the power is safely disconnected, the next step is to adjust the voltage and amperage settings on the welding machine. Refer to the machine’s manual for specific instructions on how to access and adjust these settings.
Carefully and accurately adjust the voltage and amperage to the recommended levels based on the type and thickness of the metal being welded.
Testing The Calibration
After the voltage and amperage have been adjusted, it’s important to test the calibration to ensure that the welding machine is functioning as intended.
This can be done by performing test welds on scrap metal and inspecting the resulting welds for quality and consistency. Make sure to make any necessary adjustments to the settings and retest as needed until the desired calibration is achieved.
Common Calibration Issues
When it comes to welding, ensuring that your welding machine is accurately calibrated is essential for achieving optimal results. Without proper calibration, you may encounter a range of issues that can compromise the quality and integrity of your welds.
In this section, we will explore some of the most common calibration issues that welders often encounter and provide practical tips on how to address them.
Inaccurate Readings
One of the frequently encountered calibration issues is inaccurate readings on the welding machine. This can lead to imprecise control over various welding parameters, including voltage, amperage, and wire feed speed.
To avoid this problem, follow these steps:
- Regularly check and calibrate the voltage and amperage settings on your machine. Use a reliable multimeter to measure the actual voltage and amperage output and adjust them accordingly.
- Ensure that the wire feed speed matches the settings on your machine. Use a calibrated tachometer to confirm the actual wire feed speed and adjust it if necessary.
- Inspect and clean the contact tips regularly to prevent poor electrical conductivity, which can lead to inaccurate readings.
Overheating
Overheating is another calibration issue that can significantly impact the performance and longevity of your welding machine. Excessive heat can cause premature wear and tear on crucial components, leading to frequent breakdowns and subpar welds.
To prevent overheating, consider the following:
- Maintain proper ventilation in the welding area to dissipate heat effectively.
- Ensure that the cooling system of your machine is clean and functioning correctly. Regularly inspect and clean the cooling fans and replace any faulty components as needed.
- Monitor the duty cycle of your welding machine and avoid exceeding the recommended operating limits. Overworking the machine can lead to excessive heat buildup.
Electrode Sticking
Electrode sticking is a frustrating issue that can hamper your welding process and compromise the quality of the welds. When the electrode sticks, it can cause uneven arc starts, splattering, and inconsistent penetration.
To prevent electrode sticking, consider the following tips:
- Check the electrode stickout regularly and ensure that it complies with the manufacturer’s guidelines. Incorrect stickout can contribute to electrode sticking.
- Clean the workpiece surface thoroughly before welding to remove any contaminants that may hinder smooth electrode movement.
- Use an appropriate electrode angle and maintain proper travel speed to minimize the likelihood of electrode sticking.
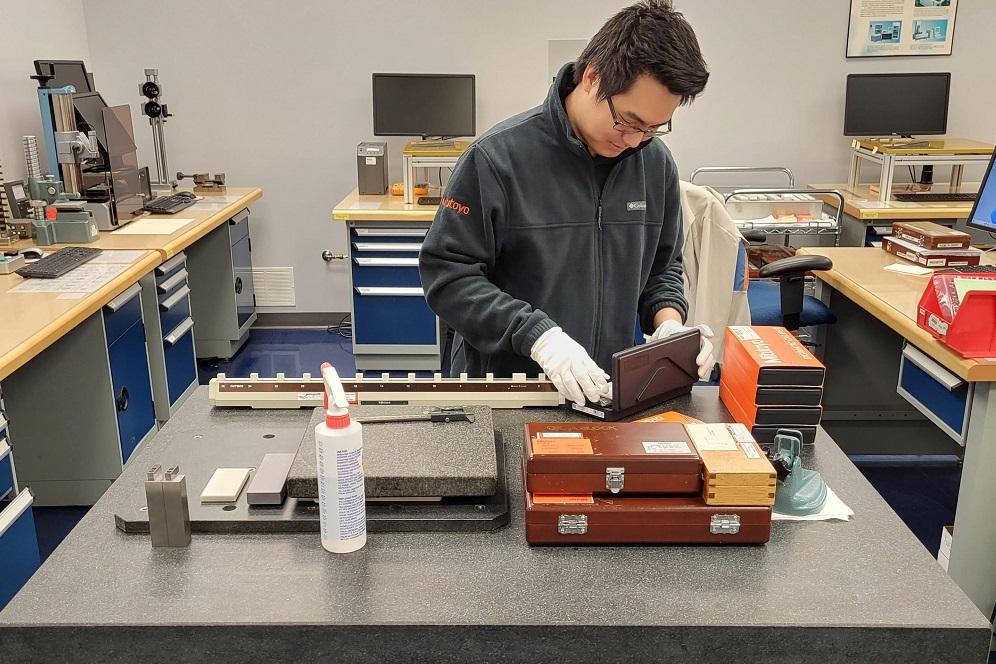
Tips For Successful Calibration
To successfully calibrate a welding machine, start by ensuring all components are clean and in good condition. Follow the manufacturer’s guidelines for the specific machine, using the correct tools and techniques.
Perform regular checks and calibrations to maintain optimal performance and prevent potential issues during welding operations.
Regular Maintenance
Regular maintenance is key to ensuring that your welding machine is calibrated correctly. By performing routine checks and upkeep, you can prevent any major issues that could affect the calibration of the machine.
Cleaning the machine regularly and removing any dirt or debris is important for accurate calibration.
Additionally, inspecting the cables, connections, and electrodes for any signs of damage or wear and tear can help to identify and fix any potential problems before they impact the calibration.
Following Manufacturer Guidelines
It is crucial to always follow the manufacturer’s guidelines when calibrating your welding machine. The manufacturer knows their equipment best and provides specific instructions for calibration, ensuring optimal performance and accuracy.
Refer to the owner’s manual or any documentation provided by the manufacturer for detailed steps and recommendations.
By adhering to these guidelines, you can be confident that you are calibrating your welding machine correctly and maintaining its precision.
Benefits Of Calibrating Welding Machine
Calibrating a welding machine comes with various advantages that ensure optimal performance and longevity of the equipment.
Improved Weld Quality
Calibrating your welding machine ensures consistent and precise welds.
- Reduces the risk of defects
- Enhances overall weld quality
Extended Equipment Lifespan
Proper calibration extends the lifespan and functionality of your welding machine.
- Prevents premature wear and damage
- Saves costs on repairs and replacements
Frequently Asked Questions For How To Calibrate Welding Machine
How Welding Machines Are Calibrated?
Welding machines are calibrated by adjusting voltage and wire feed speeds for accurate performance. Calibration ensures precise welding results.
What Is The Standard For Welding Calibration?
The standard for welding calibration is set by international organizations, such as the American Welding Society (AWS).
It involves ensuring that welding equipment and processes meet specific criteria to produce high-quality and reliable welds. Calibration ensures accuracy and consistency in welding operations.
How Do You Calibrate A Miller Welding Machine?
Calibrating a Miller welding machine is important for optimal performance.
To do it, follow these steps:
(1) Check the machine’s manual for specific instructions.
(2) Verify the machine’s power source.
(3) Adjust the voltage and wire feed speed settings according to the welding application.
(4) Test the weld with quality parameters in mind.
(5) Fine-tune the settings as needed.
How Do You Adjust Welding Current?
Adjust welding current by turning the dial on the welding machine. Increase or decrease until desired level.
Conclusion
Calibrating your welding machine is crucial for precise and efficient welds. Proper calibration ensures safety and high-quality work results.
Follow the steps outlined for accurate calibration. Regular maintenance and calibration will prolong the lifespan of your welding equipment. Stay informed and empowered in your welding endeavors.